自分でオリジナルマフラーを造りたい
DIYでオリジナルマフラーを造る。
これはボクが昔からやってみたいことのひとつです。
過去にはバイクのサイレンサーを流用したマフラーを、図面を描いて試作屋さんに加工してもらい、
ビートに装着していたこともありました。
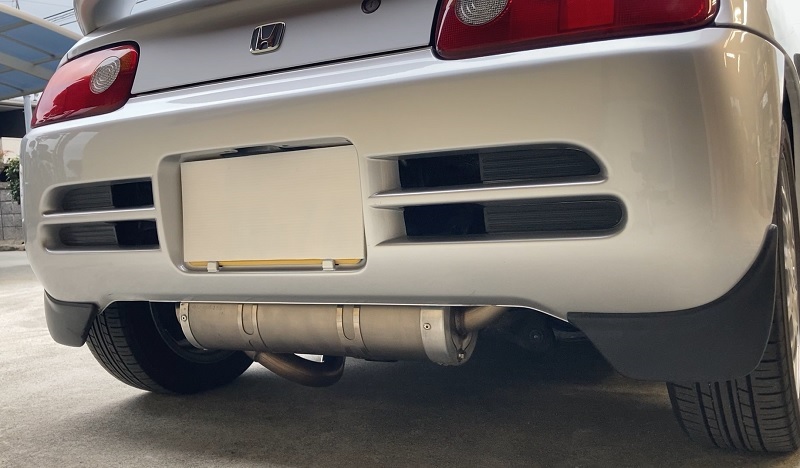
ワンオフの一品物ではありますが、完全なオリジナルかと言えばそうではありません。
ゼロから考えたオリジナル仕様のマフラーを、できる限り自分で加工して造ってみたいですよね。
↓ブログ村ランキングにポチッとご協力をお願いします!

にほんブログ村

にほんブログ村
マフラーの製作手順
マフラーの製作は大きく分けると4工程で進めて行きます。
①設計 ②材料手配 ③加工 ④確認
設計
設計とは頭の中にあるイメージを見えるようにして
第三者に伝えられるようにすることだと思って下さい。
具体的にやることは「デザインと仕様を決める」「部品のメモを描く」ことです。
デザインを決める
どんなマフラーにしたいのか?頭の中にあるイメージを整理します。
ボクが造りたいマフラーは、
・街乗りでの使いやすさ → トルク重視の出力特性
極力管長を長く取れるようにしつつ、加工のやり易さも考えて、
ループを描くレイアウトに決めました。
・バリバリとした破裂音のしない甲高い排気音
→ サイレンサーはストレート構造でグラスウールで吸音
・サイレンサーは低重心を狙ってループの下側に配置。
バンパーの下からチラ見せしつつ、テールパイプは助手席側に出すデザインにします。
仕様を決める
マフラーの取り回しが決まったら、仕様を決めていきます。
パイプサイズ
パイプサイズは悩みどころです。
闇雲に太くしても低中速域がスカスカになってしまうので、
排気量が660ccのビートの場合、Φ40~Φ50位が妥当なところでしょう。
手元にあるワンオフマフラーはΦ48.6mm、無限ツインループはΦ45mm、
巷で有名な「魔夢管」はΦ42.7mmと、だいたいΦ42.7~Φ48.6のパイプを
採用しているようです。
今回は、ボクがリスペクトしている「魔夢管」に倣って、Φ42.7mmで造ります。
管長
管長については、トルクが出るようにしたいので、出来るだけ長くできるようにしていきます。
今回はマフラーのフランジ部分からテールパイプ出口まで約2メートルの管長になりました。
消音方法
消音方法はパンチングパイプとグラスウールを組み合わせたストレート構造にします。
理由は構造がシンプルで造りやすいのと、騒音規制値内で迫力のある音にしたかったからです。
ストレート構造の他にはサイレンサーの内部を複数の部屋に分割して消音する
「反転膨張式」がありますが、消音効果が大きい反面、排気抵抗や重量が増すのがデメリットですね。
それに部品点数も増えるので、造る手間も費用も増えてしまいます。
材質
材質はステンレスにします。
マフラーの材料としては、鉄、チタン、アルミ等もありますが、
耐久性と加工のし易さとコストを考えて、総合的にバランスの良いステンレスにしました。
部品のメモを描く
マフラーを造るには部品を造らないといけません。
具体的にはパイプを曲げて、ステンレスの板を加工して部品にしていきます。
ぜんぶ自分で加工できればいいのですが、パイプ曲げや、板のプレスには設備も必要なので、
今回は設計図を描いてプロに依頼します。
設計図と聞くと難しそうな印象がありますが、本格的な図面でなくても、
部品の形が伝わるように寸法が書いてある「設計メモ」でも物は造れます。
今回は設計メモを描くために「無限ツインループ」をお手本にして寸法を測っていきます。
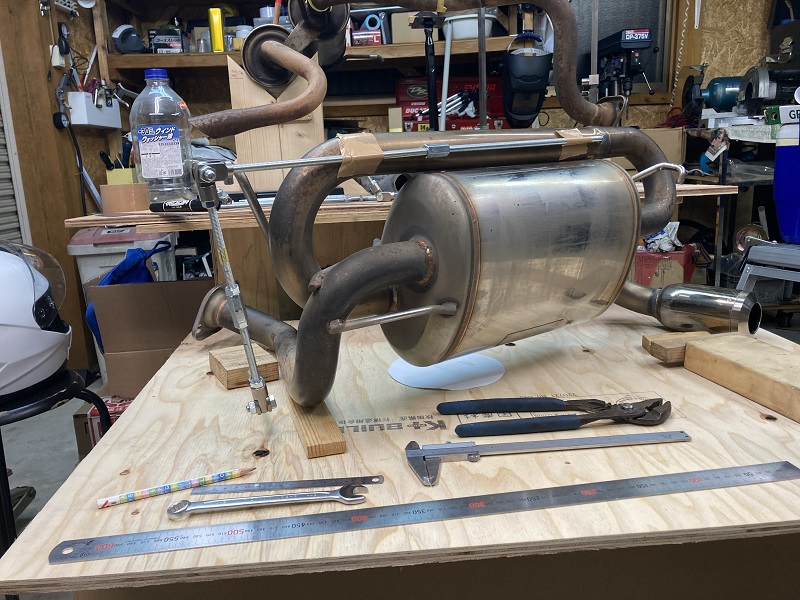
寸法取り
マフラーを造る上でパイプの曲げ加工は必ず必要になってくるので、
寸法取りは主にパイプの測定が作業の中心になります。
マフラーの曲がったパイプを図面にするのは一見難しそうですが、
曲げの部分だけに注目すると、単純で分かりやすいと思います。
クネクネ曲がったパイプは複数の曲げ加工の集合体です。
3ヶ所曲がっていれば、曲げの部分毎に3回曲げているだけなんです。
また、パイプ曲げは平面上で行われる加工なので、パイプの曲がった部分を平面にして、
「曲げ角度」(何度曲げているか)と「曲げ半径」(いくつの半径で曲げているか)を調べれば、
曲げの形状はメモにすることができます。
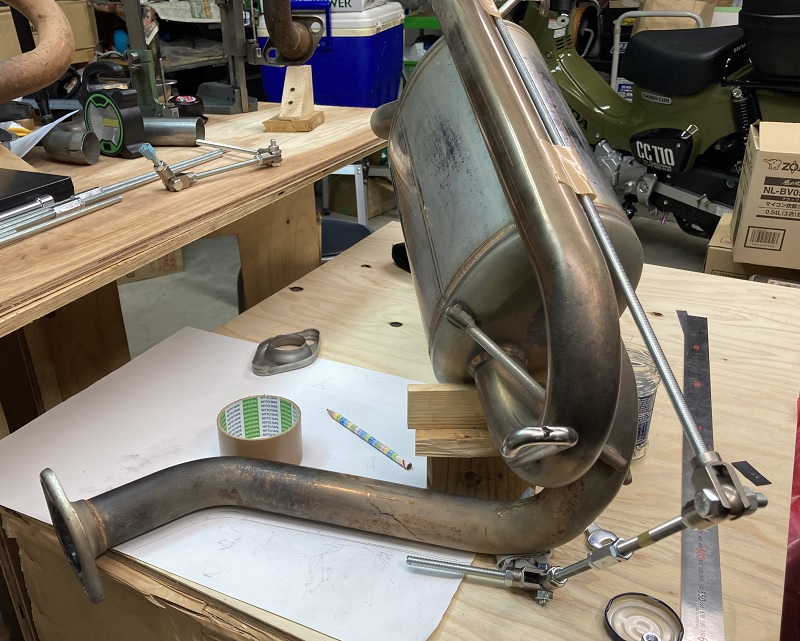
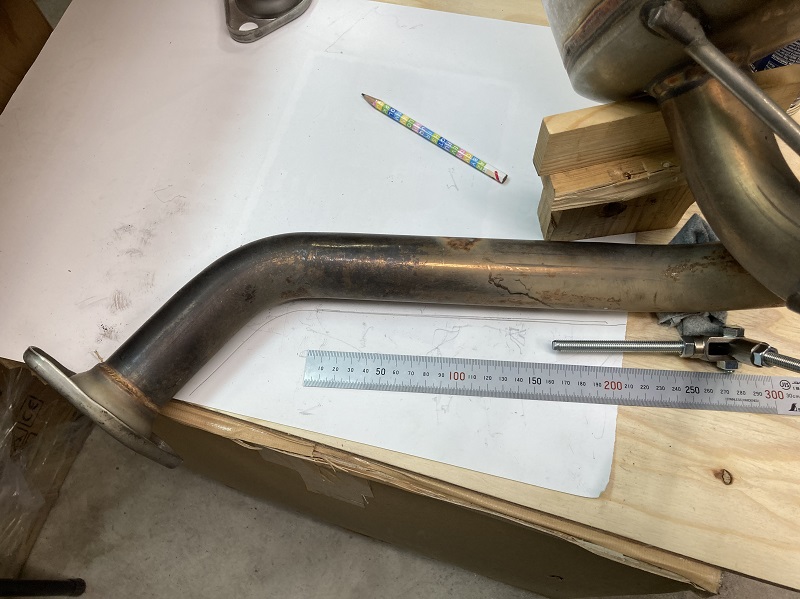
2曲げ目・3曲げ目は無限のマフラーと形状が違うので1曲げ目の方法が使えません。

そこで、エアーシリンダ用の「ナックルジョイント」と「M8の全ネジ」を使って擬似的に
パイプの曲げを再現することで、曲げ角度を決めていきます。
内パスに角度を移してから、
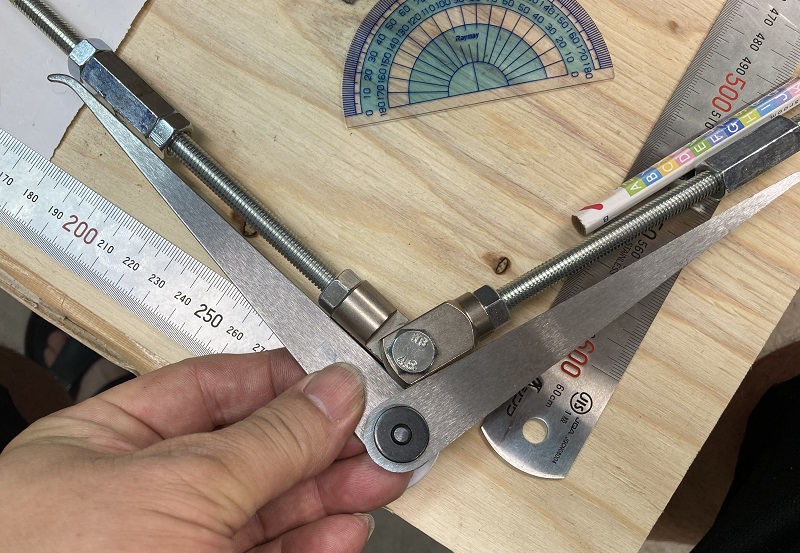
分度器で角度を確認します。
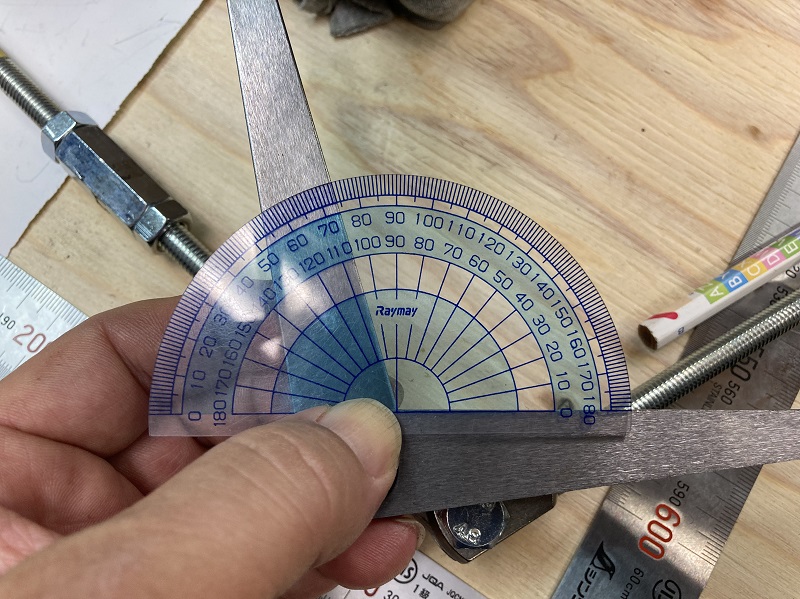
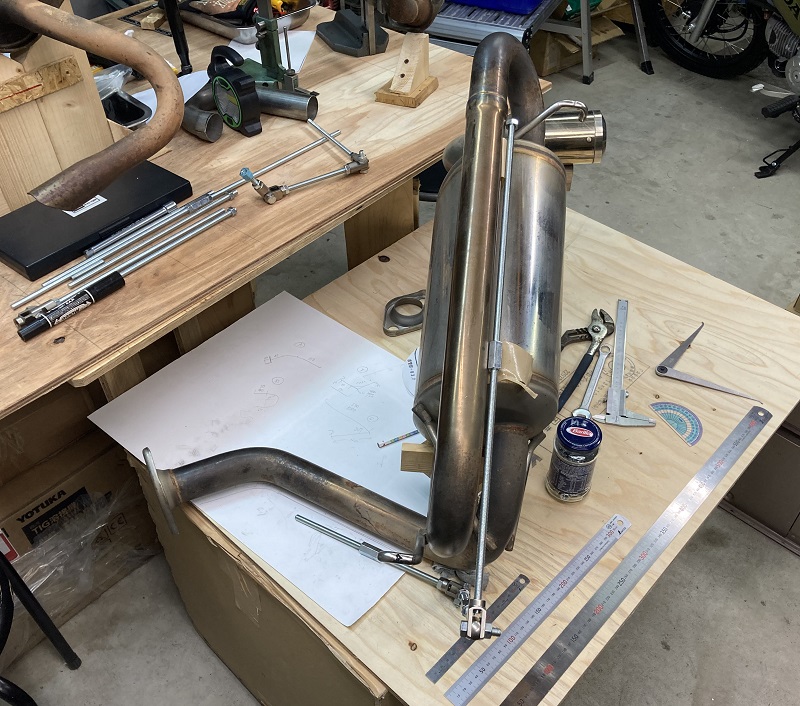
パイプの直管部分はスケールで測ります。
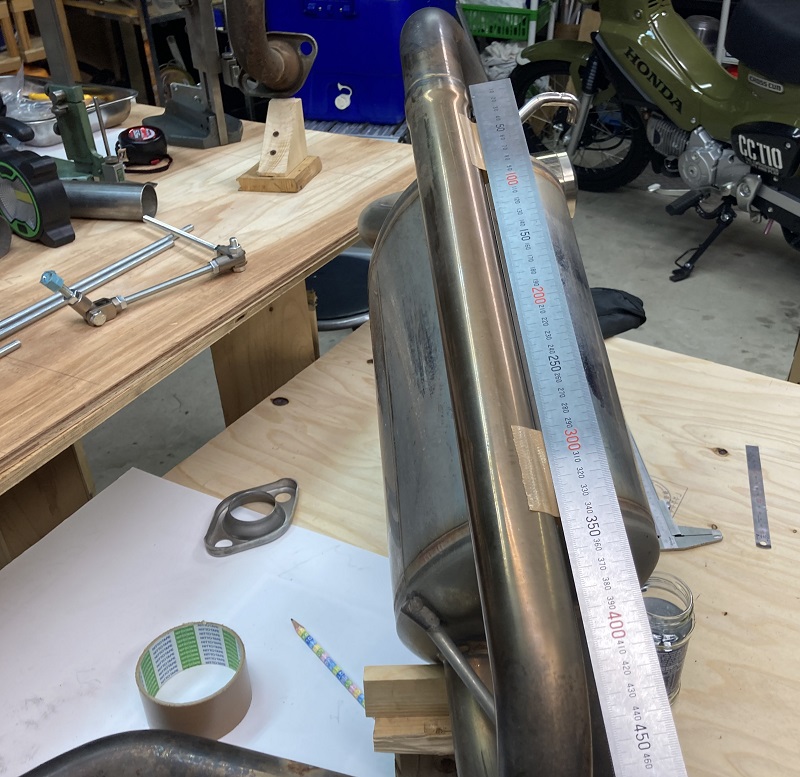
400mmですね。
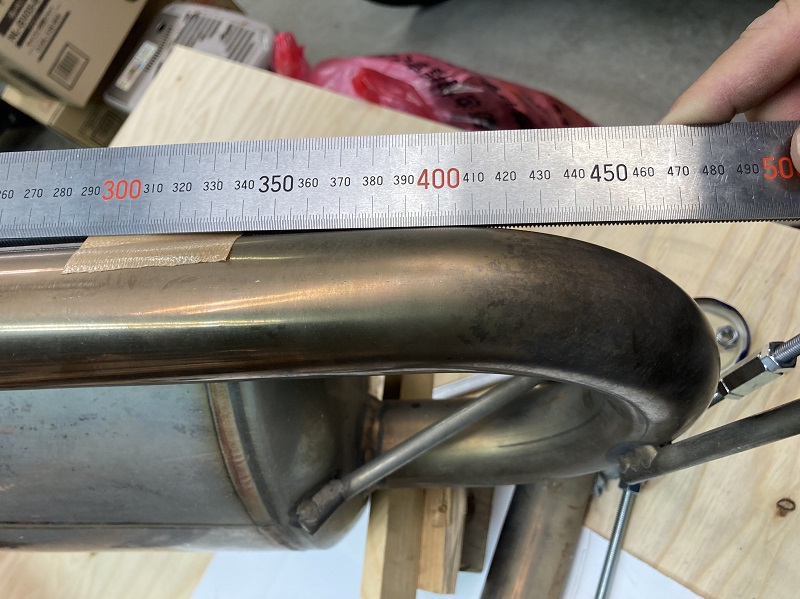
無限のマフラーボディは300mmでした。
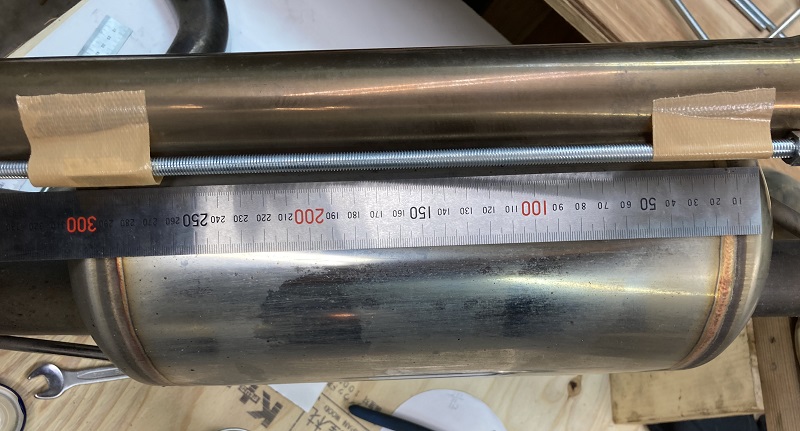
測った値はとりあえずメモしておいて、部品毎に設計メモにしていきます。
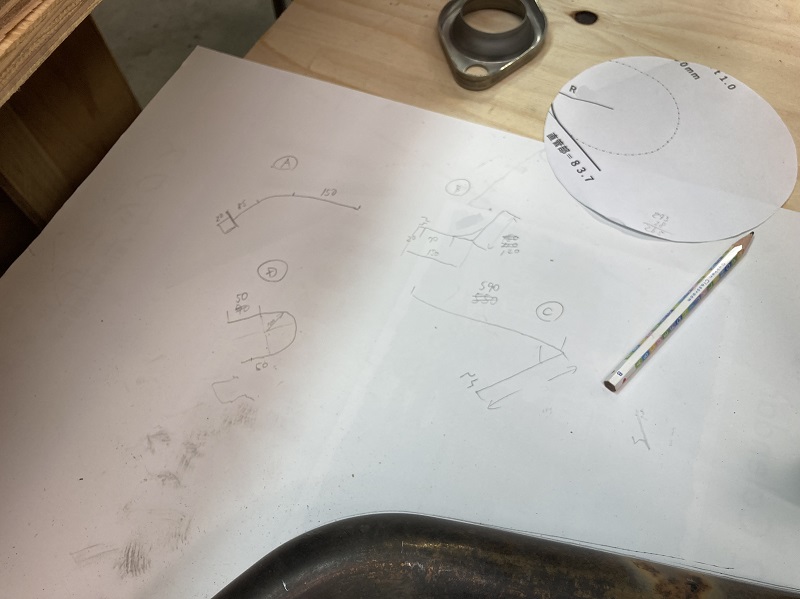
ちなみに今回は曲げの部分毎にパイプを分割した設計にしました。
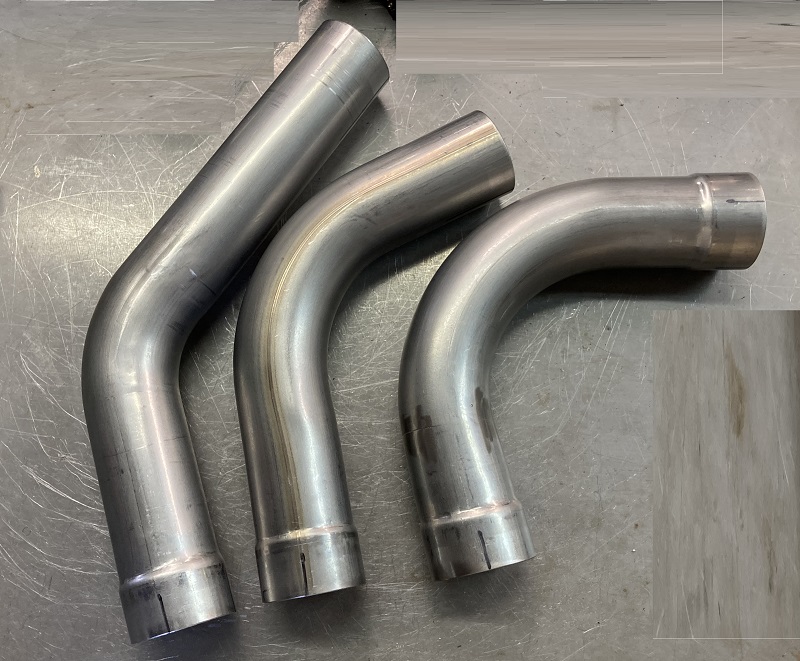
理由は2つです。
1)分割していると組んでいく途中で切ったり繋いだりして寸法を調整できる
2)1曲げの場合、曲げ治具が不要になるので安くなる
バラバラのパイプを溶接する手間はありますが、車体側の寸法が分からないので、
ワンオフする時はこの方法がオススメです。
材料手配
材料手配は、単品部品の製作依頼や、ネットで注文できる部品や素材を購入します。
単品部品の製作は、昔からお世話になっている試作屋さんにお願いしました。
また、グラスウールやステンレスウール、球面ジョイント等、
市販されているものは、Amazonや楽天で買いました。
曲げ加工済のパイプなどもネット通販で購入できるので、インターネットは便利ですね。
加工
試作屋さんに加工をお願いしてから約1か月で部品が届きました。
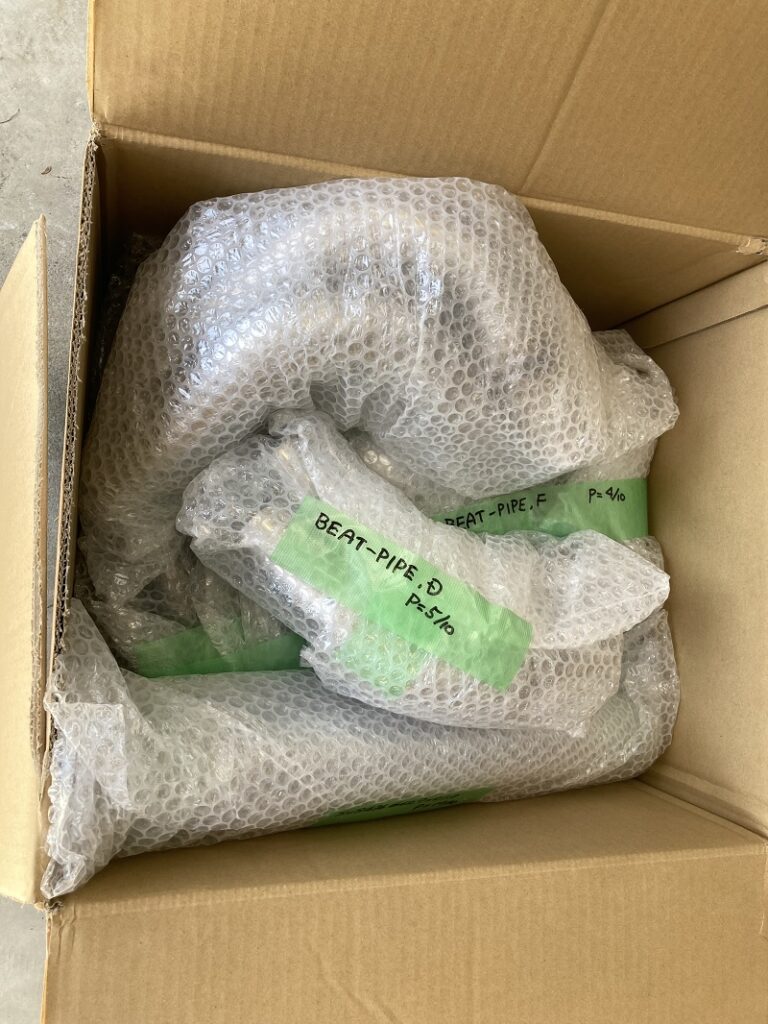
素晴らしい出来栄えです。
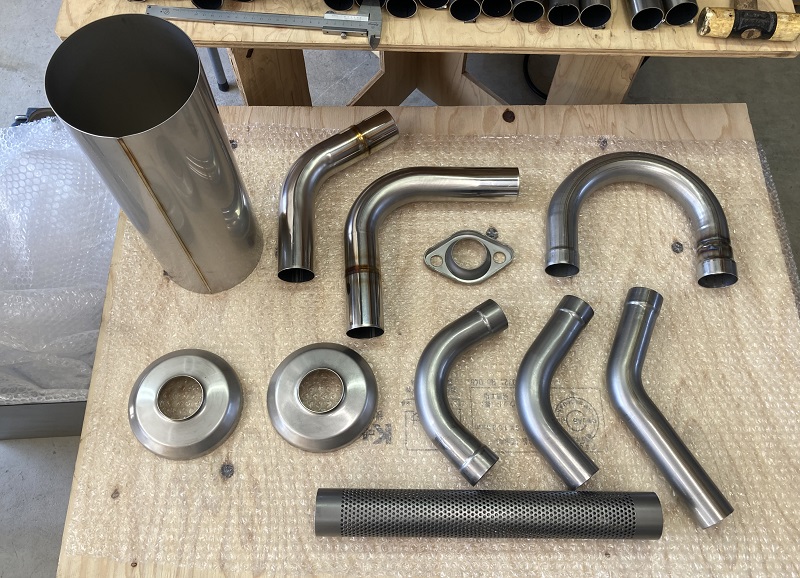
仮組してみました。イメージ通りです!
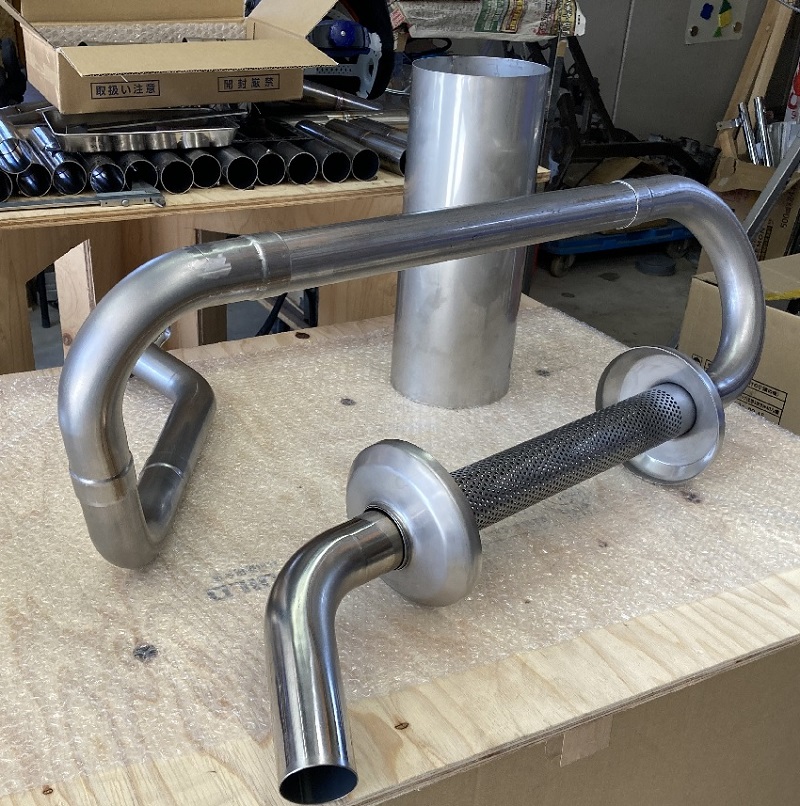
さっそく組み立てを始めます。
組み立ての手順としては「エキパイ」「サイレンサー」「ステー」の順番で組んでいきます。
エキパイの組み立て
まず球面フランジを取り付けて、1曲げ目のパイプを合わせてみます。
フランジへの差し込み代を調整しつつ、パイプを固定する角度を決めてからマジックで印をつけます。
印を付けたら、フランジを取り外してからフランジと1曲げ目のパイプを溶接で仮付けします。
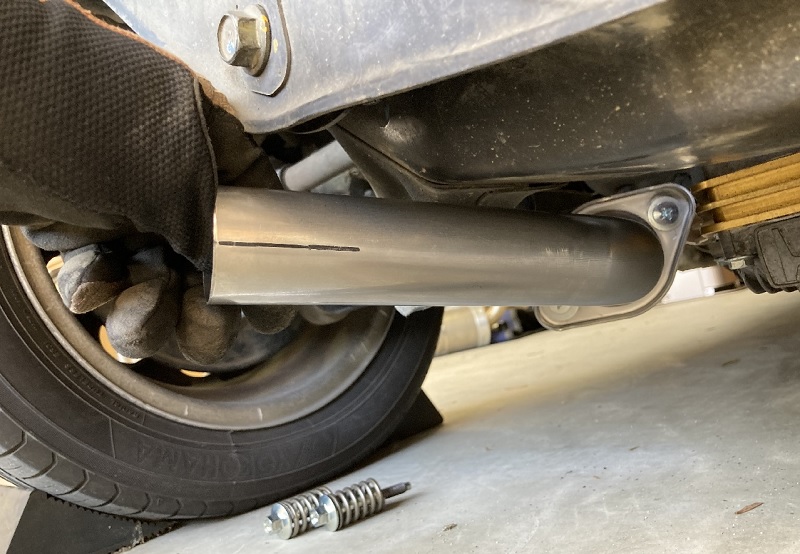
この要領で2曲げ目、3曲げ目を仮付けしていきます。
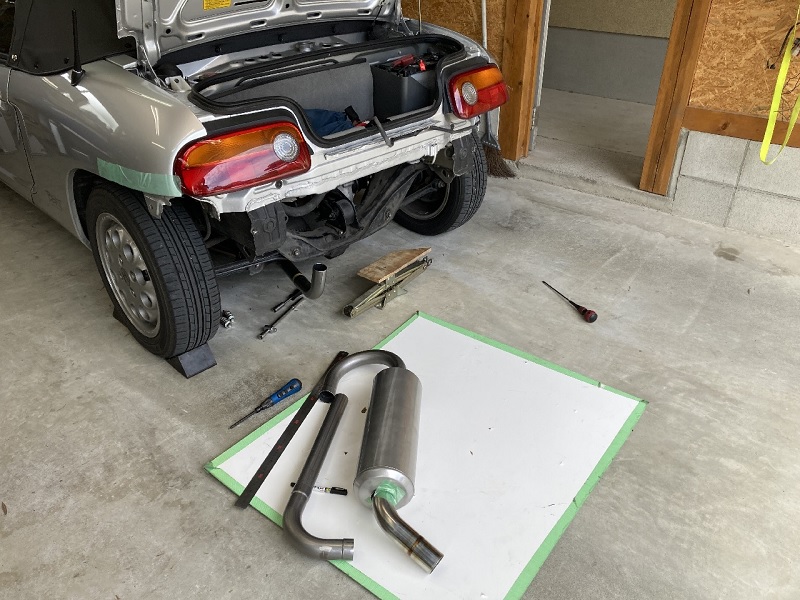
1曲げ目の2曲げにつながる部分が長いのでカットします。
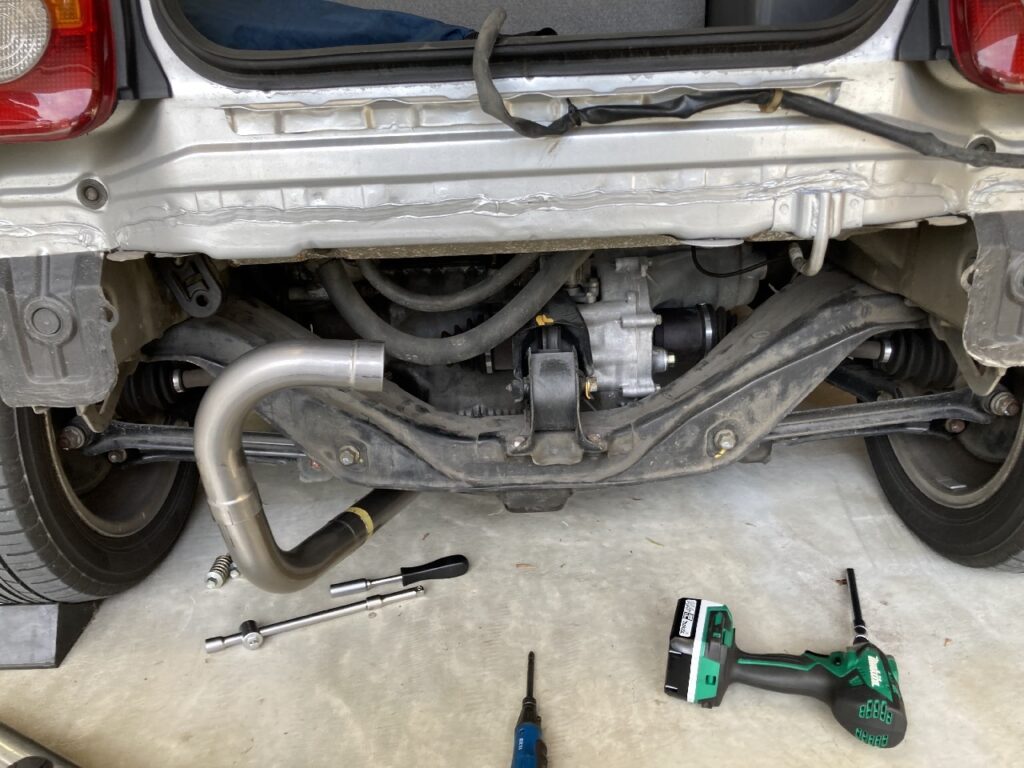
長すぎる部分は、短く切って調節していきます。
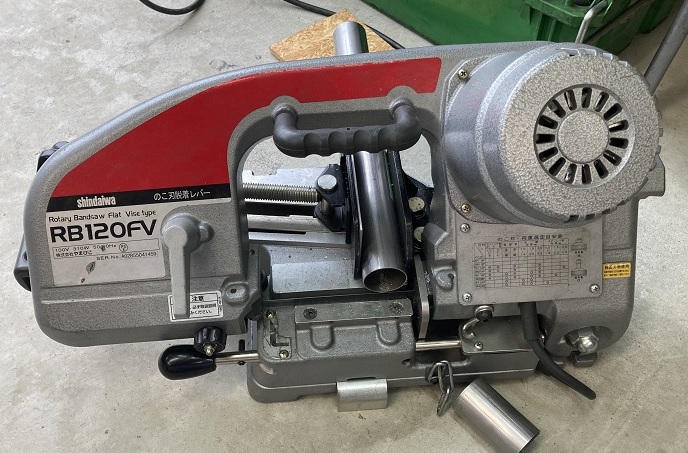
クリアランスを確保しながらできるだけ管長を延ばせるようにしていきます。
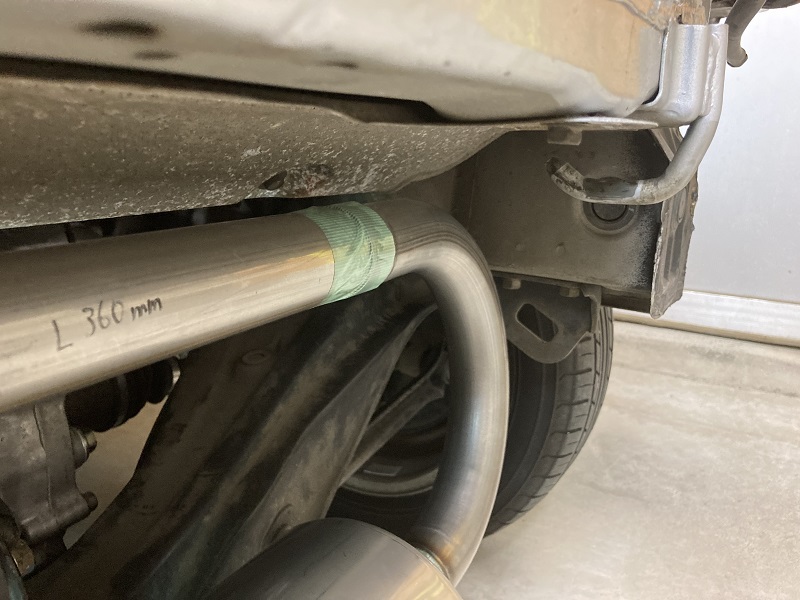
切ったり繋いだりして、フランジからサイレンサーの部分までのパイプを仮付けしました。
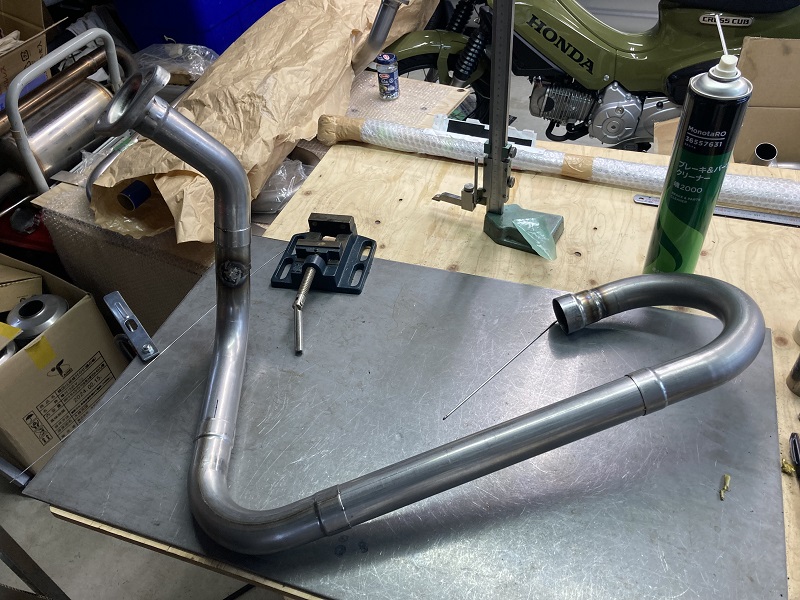
車体に仮組してみます。カッコいい!!
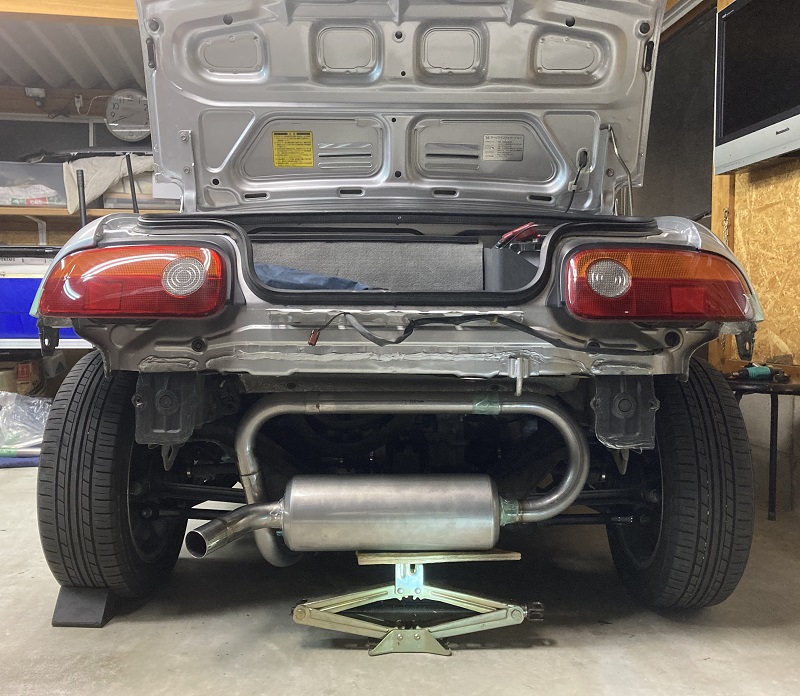
バンパーを着けるとこんな感じです。
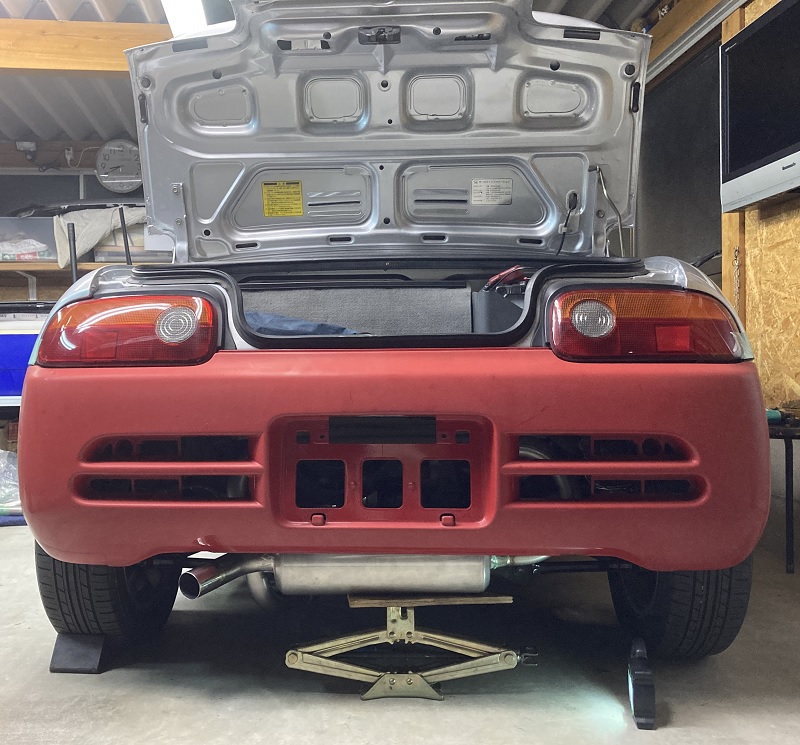
仮組段階で、車体各部分とのクリアランスを見ておきます。
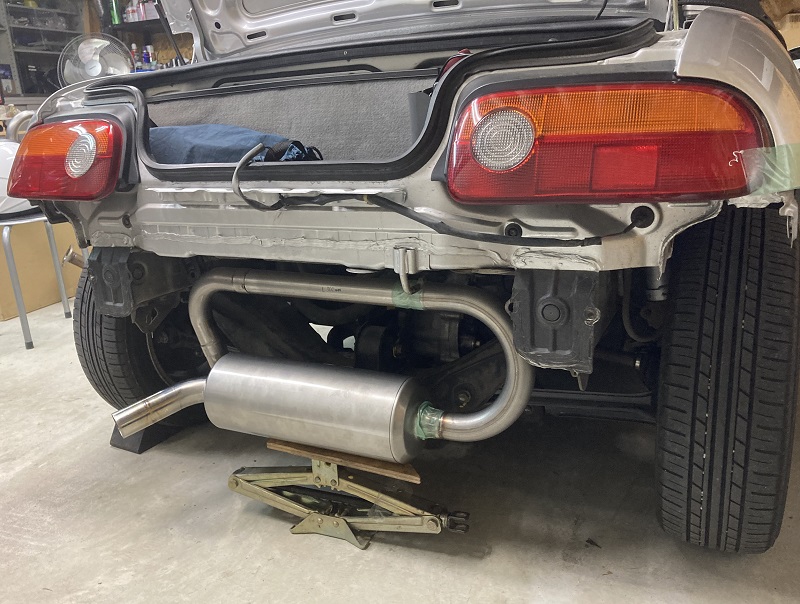
サイレンサーとエンジンマウント。ちょっと近いかな?でも無限もこんな感じだったのでヨシ!
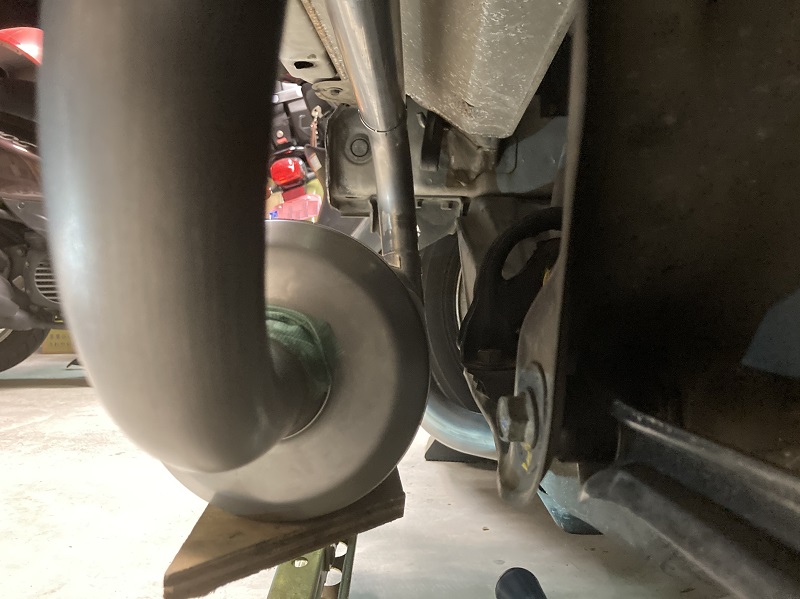
エンジンメンバーとエキパイ部分のクリアランスは十分取れててヨシ!
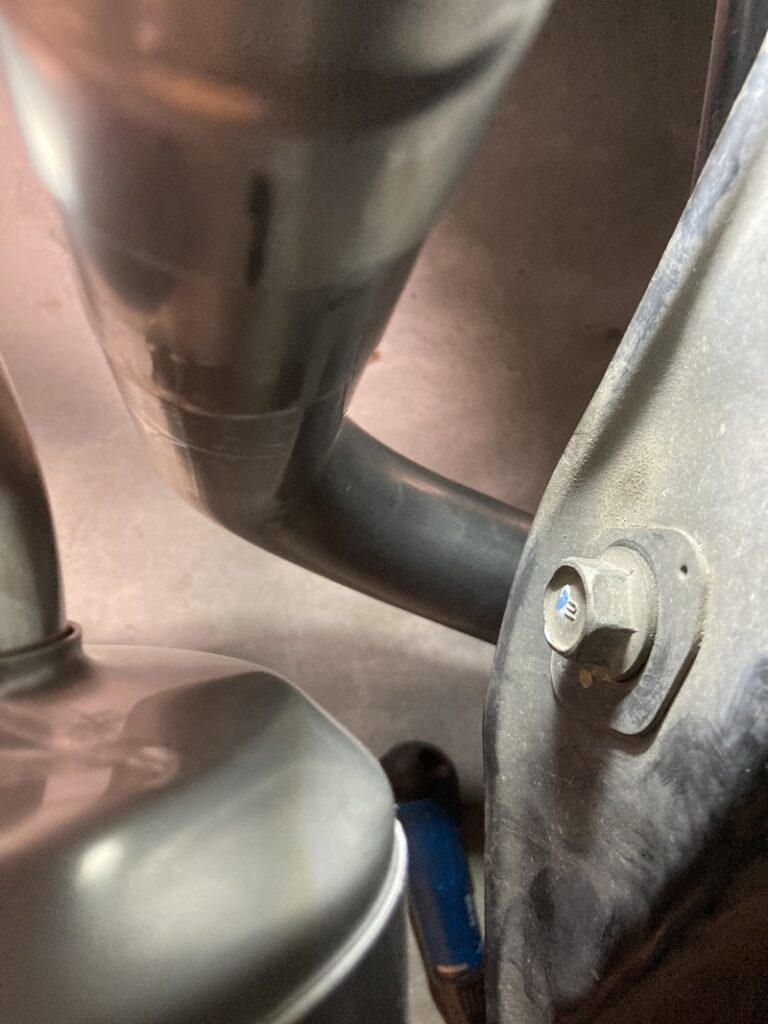
サイレンサーの組み立て
サイレンサーを組んでいきます。
始めにサイレンサーのボディと片側のキャップを仮付けしておきます。
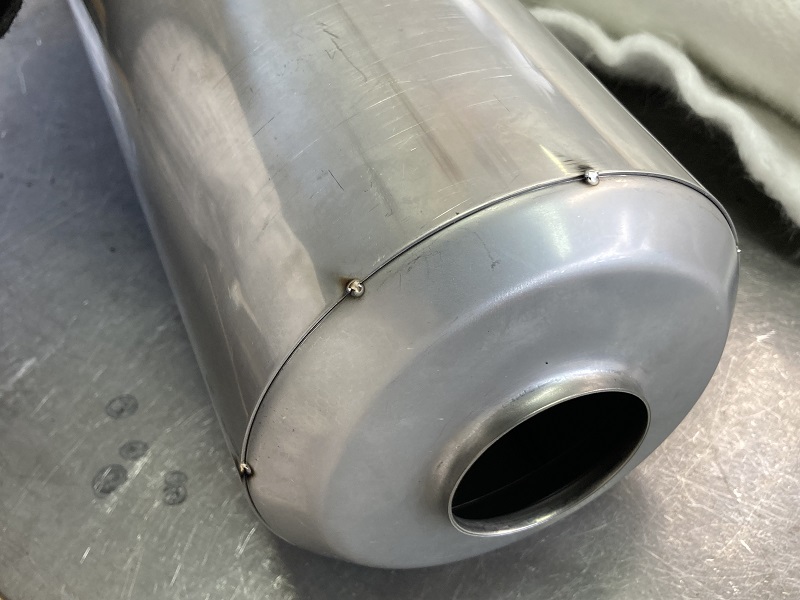
インナーパンチングパイプにステンレスウールを巻いていきます。
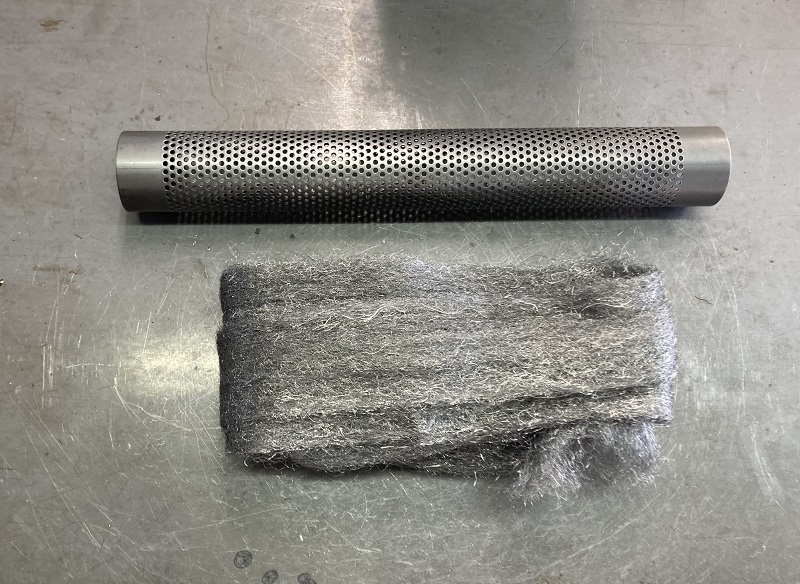
ステンレスウールを巻くことで、グラスウールの飛散を抑えてくれます。
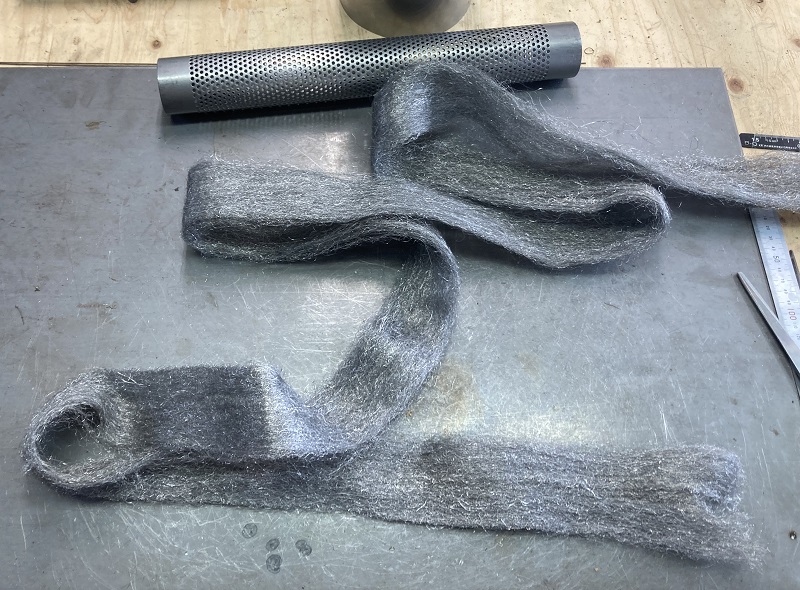
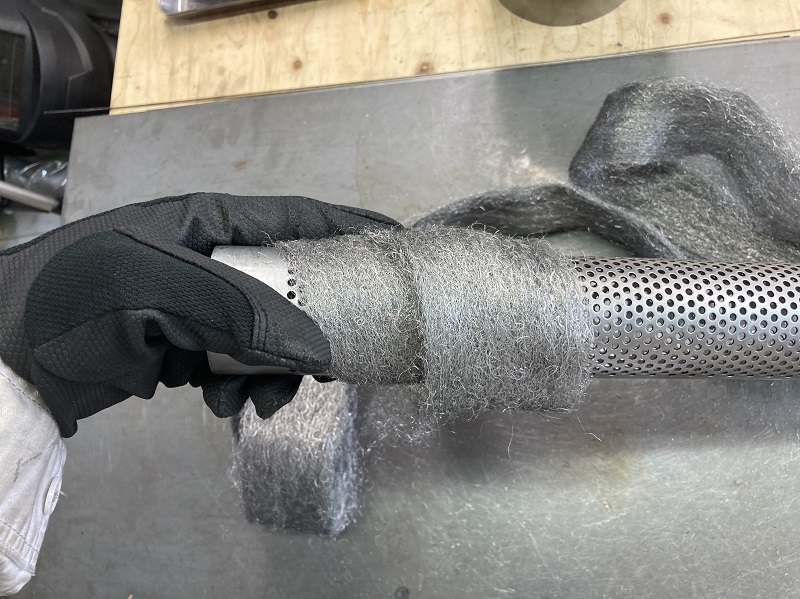
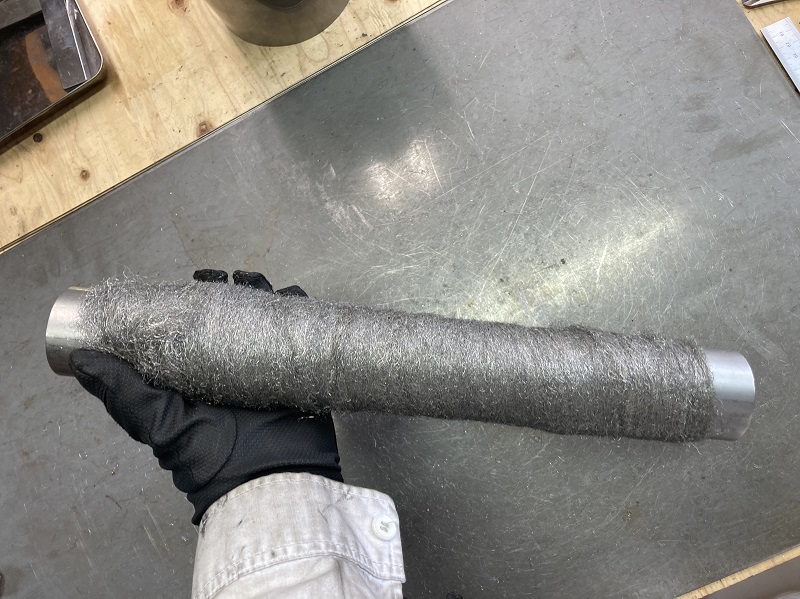
ステンレスウールを巻いたら解けないようにマスキングテープで留めておきます。
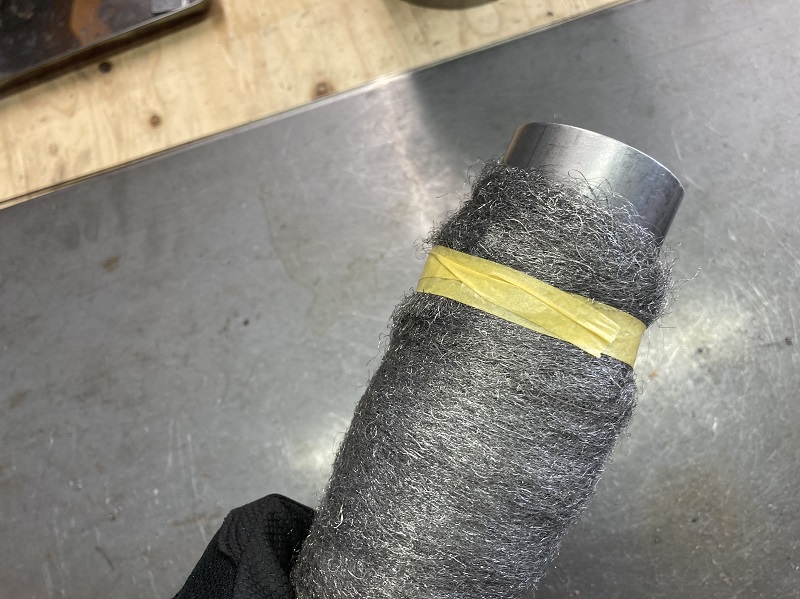
次にグラスウールを巻いていきます。
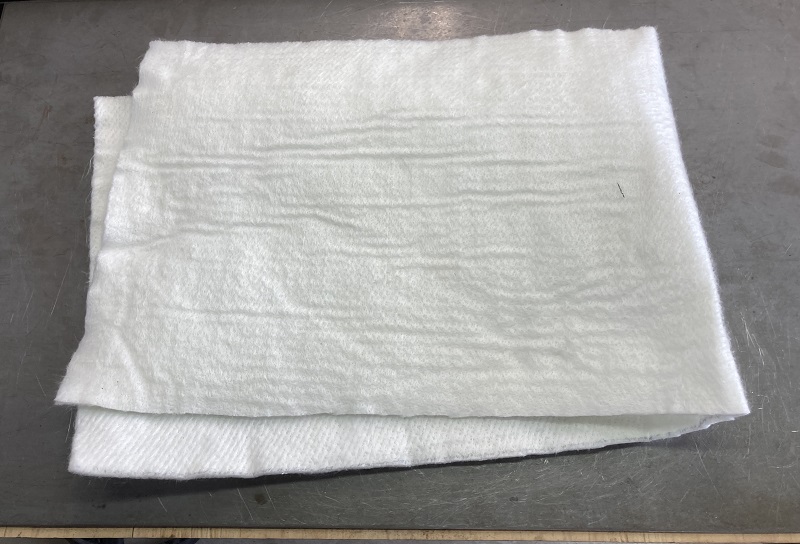
サイレンサーボディの内径はΦ137mmです。
グラスウールをインナーパイプに巻いていきますが、サイレンサーの中を一杯にするために
厚さ7mmのグラスウールを1400mm使いました。
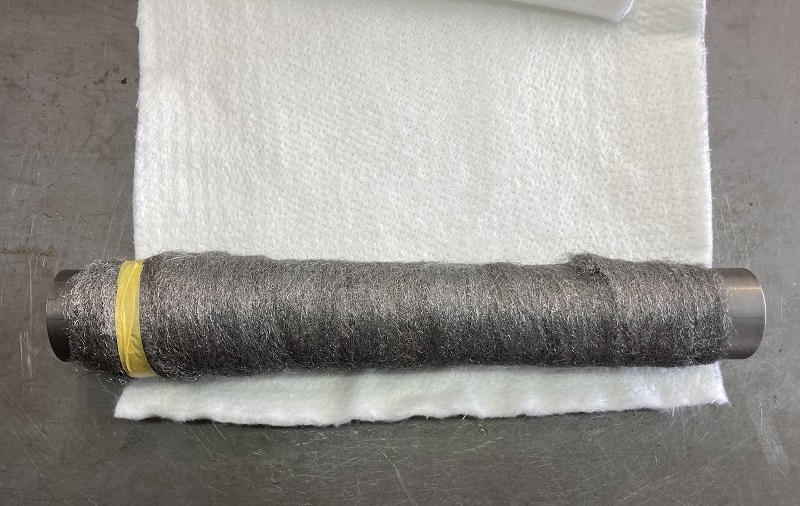
巻き終わりました。
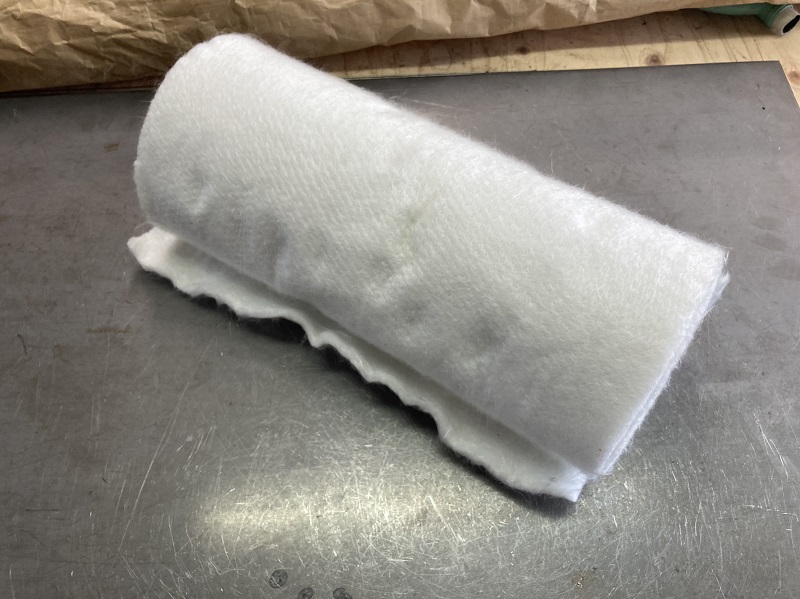
ボディに詰めていきます。
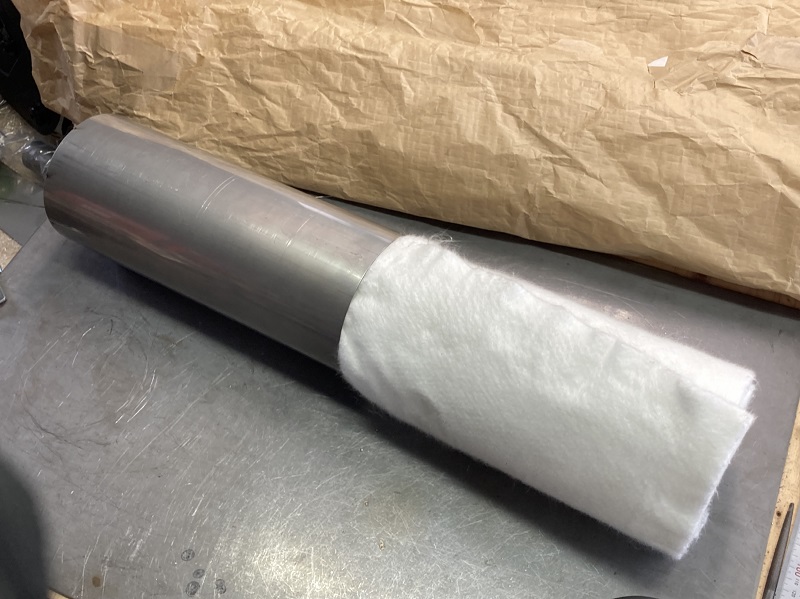
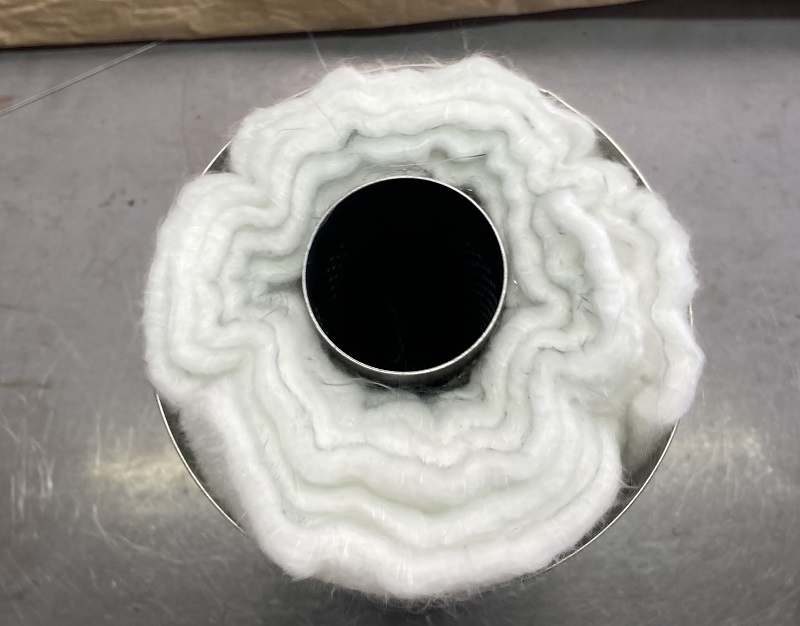
キャップ裏面にもグラスウールを詰めておきました。
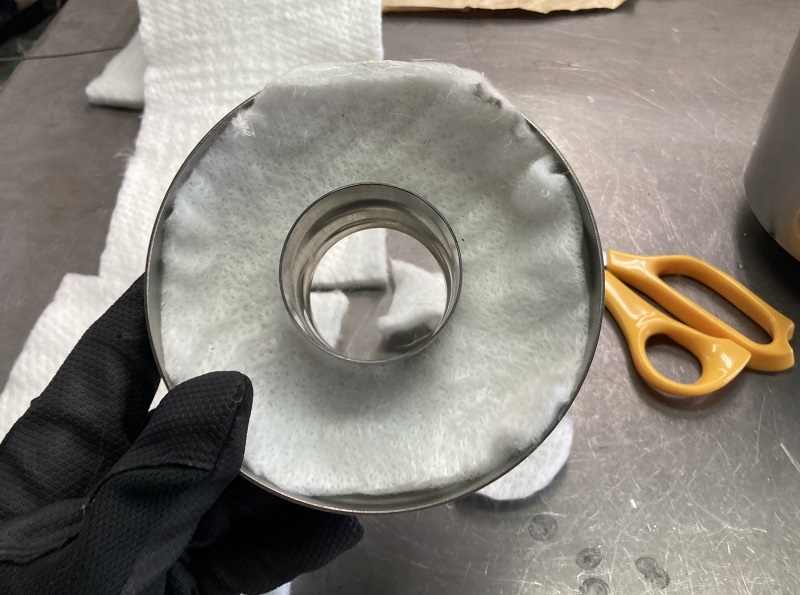
巻きあがったものをボディに差し込んで、残りのキャップで蓋をします。
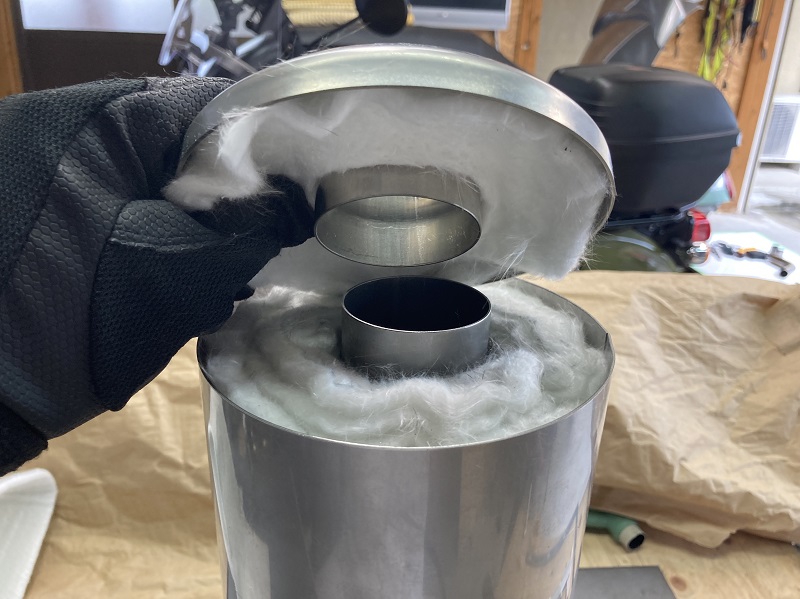
蓋をしてから仮付けして本付け溶接しておきます。
マフラーステーの組み立て
ステーにはSUS304のΦ10丸棒を使います。
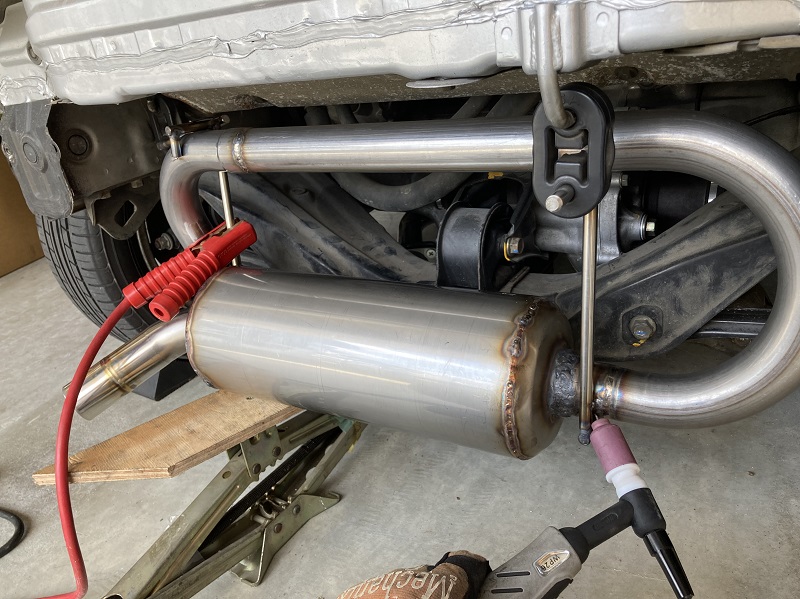
吊りゴムで引っ掛けるので多少のズレは許容範囲ですから、現物合わせで材料を切って繋ぎます。
ここで問題になるのが溶接です。
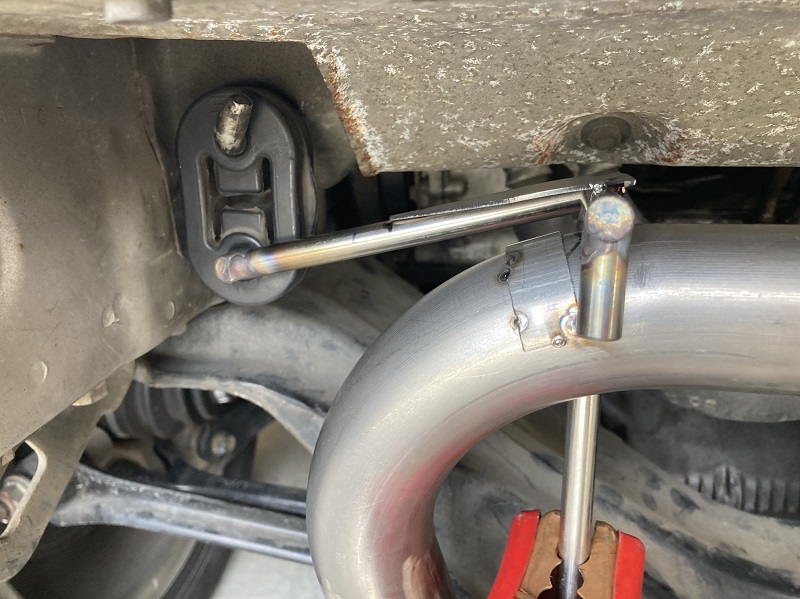
エキパイやボディ等、ステーを溶接したい部分は板厚が1mmなので、
Φ10の丸棒を溶接するには、かなりの溶接技術が必要です。
(板厚の差が大きいと、厚い方が溶ける前に薄い方が溶け落ちて穴が開いてしまう)
ボクはまだ、そのような溶接技術がないので、丸棒をつないで作ったステーにして
最小限の溶接でパイプとステーを固定しました。
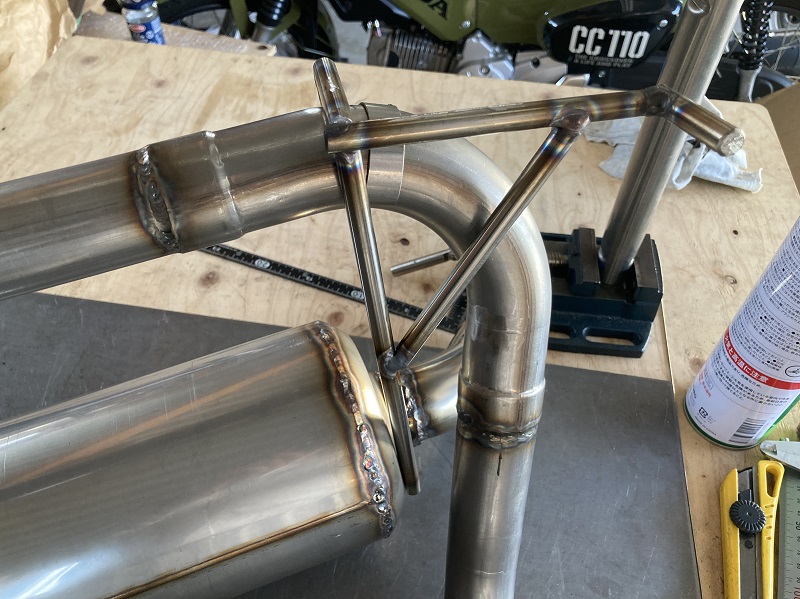
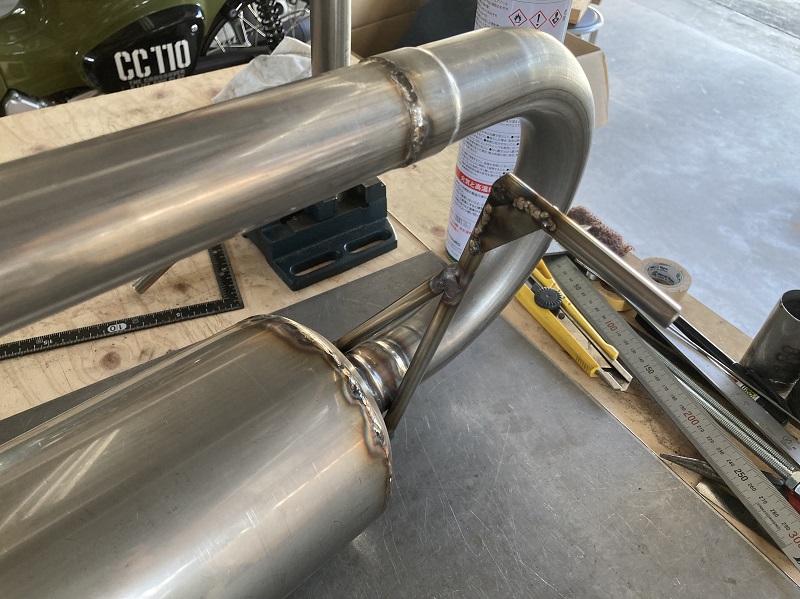
完成
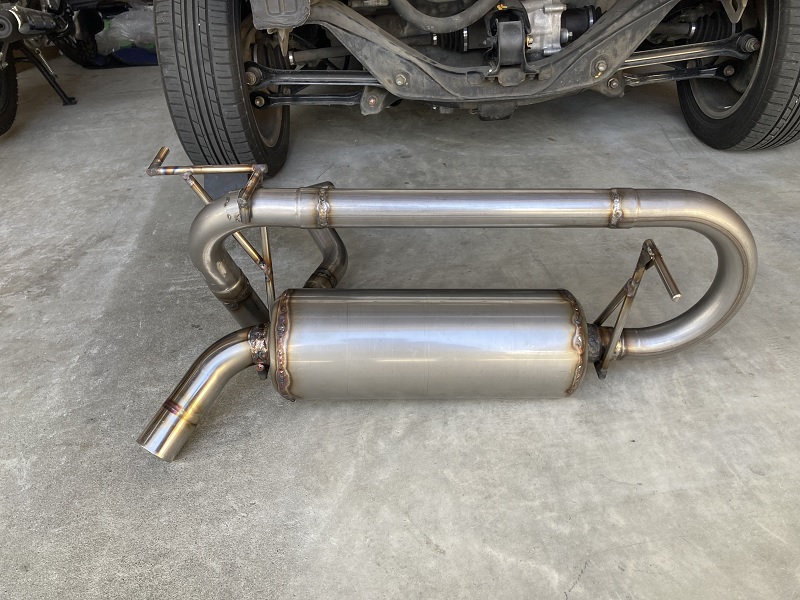
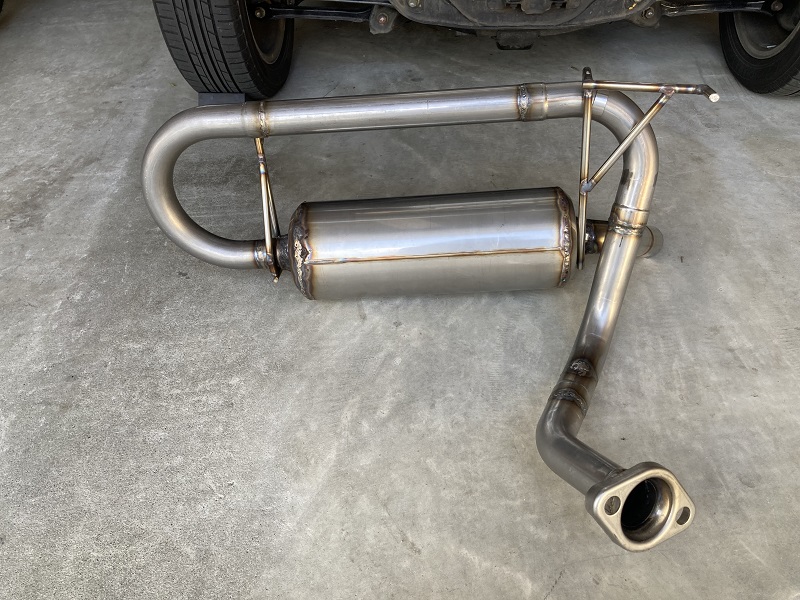
確認
・取り付け確認
出来上がったマフラーをビートに取り付けます。
干渉する部分等はありませんでした。
しかし、バンパーを合わせて見ると、水平にデザインしたはずのサイレンサーが
左下がりの斜めになっています。
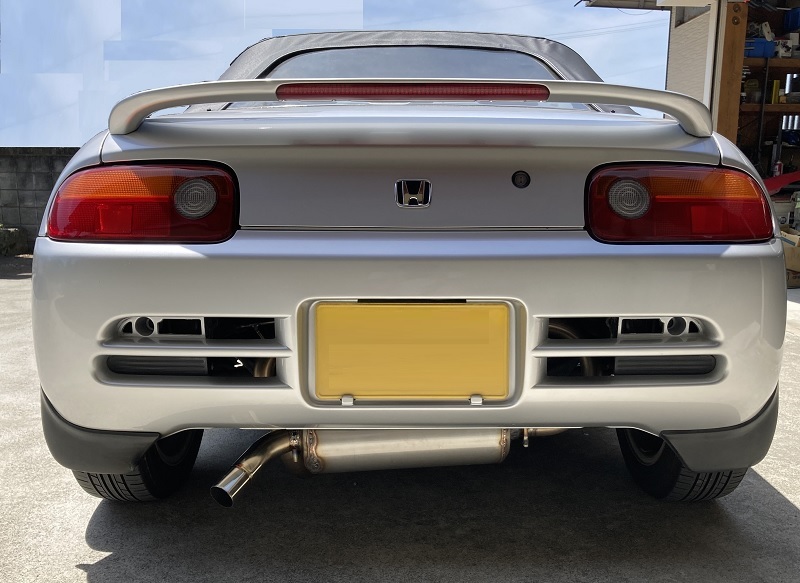
どうやらエキパイとサイレンサーを傾いた状態で溶接してしまったのと、
溶接がうまく行かず、何度もやり直したため、溶接の熱で歪んでしまったのでしょう。
現物合わせで部品がフリーな状態で溶接しているので、仕方がないですね。
その後、マフラーの吊りゴムを位置調節ができる社外品に交換して、
左下がりの状態を改善することができました。
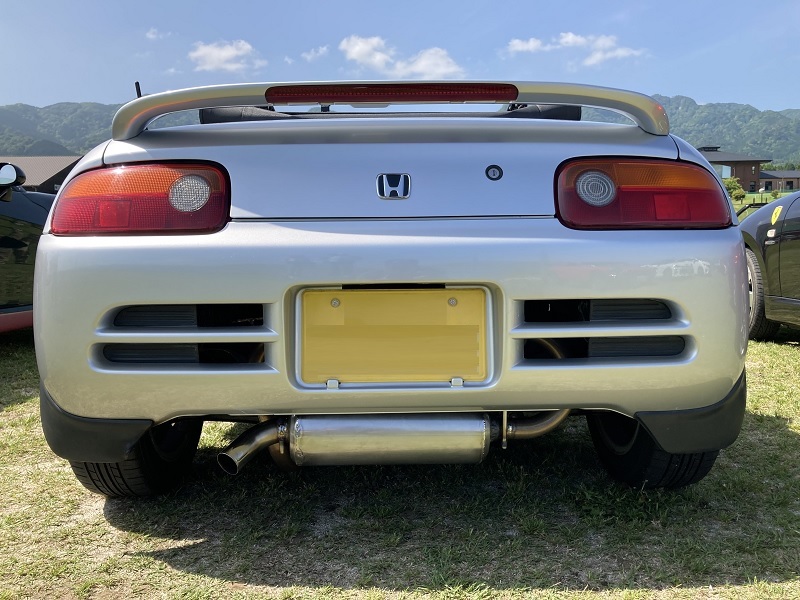
テールパイプも長さを短く詰めて、溶接焼けを落としたことで見栄えがかなり良くなりました。
音
ドキドキしながらキーを回してエンジンを始動しました。
ストレート構造なので、アイドリングの音量も上がると思っていましたが、
思いのほか静かで、拍子抜けしました。
少しの間暖気してからアクセルを煽ると5000rpm位から音に迫力が増してきて、
6000rpmをこえると低音が効いたレーシングサウンドが響きます。
バリバリ割れた音にならないか心配していたのですが、音の割れはなく、
かなり気持ちのイイ音が鳴るマフラーです。
アクセルを煽った感じでもピックアップが良くて、息つきする様な事もありません。
エンジンもスムーズに吹け上がってくれます。
近接騒音レベル
近接騒音を測定しました。
結果は
・アイドリング:88dB
・最大音量:101.9dB
※近接排気音測定の測定方法による
測定方法は、騒音計を排気の出口方向から45度の方向に、
排気管と同じ高さで50cm離して設置して、エンジン回転数を
最高出力発生時の75%で5秒間維持します。
5秒後にアクセルを急に離した時の騒音レベルを測ります。
ビートの年式の騒音規制値は103dBなので、ギリギリですが騒音規制値もクリヤできています。
まとめ
はじめての自作マフラーはTIG溶接の難しさが身に染みた1本でした。
ボクの未熟な溶接技術のせいで、職人さんが造ってくれた
素晴らしい出来栄えの部品を活かすことができませんでした。
もっと溶接を練習して経験を積む必要があります。
一方で、ある意味適当に?決めたマフラー仕様でしたが
音と性能は満足のいくマフラーになりました。
今後はパイプサイズを変えたり、サイレンサーの中身を工夫して
色々と楽しみながら、加工の技術も磨いていきたいと思います。
↓ブログ村ランキングにポチッとご協力をお願いします!

にほんブログ村

にほんブログ村
コメント